The noise control of Roots blower requires comprehensive measures from three aspects: noise source identification, propagation path blocking, and equipment optimization. The following are specific control plans and analysis:
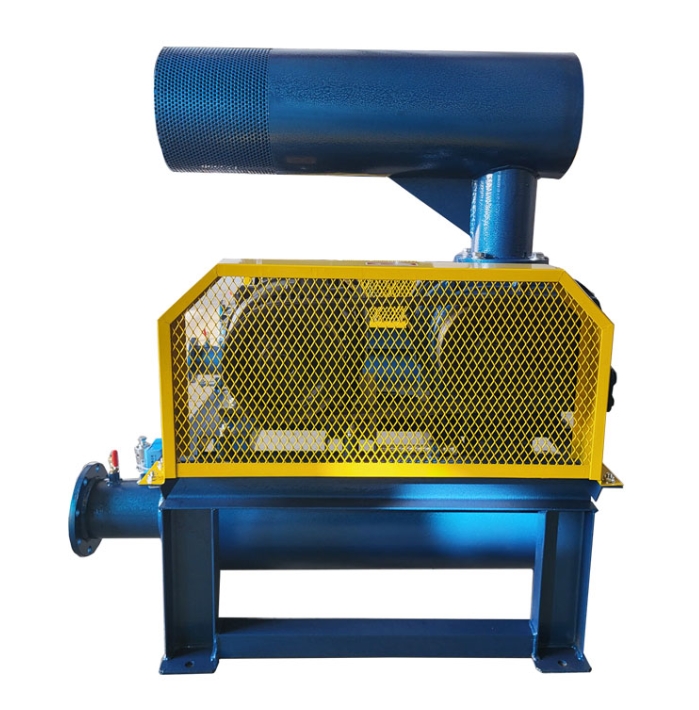
1、 Identification and Characteristics Analysis of Noise Sources
aerodynamic noise
Cause: Jet noise caused by sudden pressure changes at the inlet and outlet of the gas, as well as vortex noise caused by impeller rotation.
Characteristics: Low frequency broadband noise, with spectral peaks concentrated between 125-500Hz, and a significant increase in sound pressure level with increasing flow rate.
Mechanical noise
Cause: Vibration of components such as gear meshing, bearing rolling, and rotor imbalance.
Characteristics: Medium to high frequency noise, strongly related to speed and assembly accuracy. When the gap exceeds the tolerance, the noise intensity can increase by 10-15 dB.
Vibration noise
Cause: The vibration of the fan is transmitted to the building structure through the foundation, causing secondary radiation noise.
Characteristics: Low frequency noise (≤ 200Hz), long propagation distance, and solid sound transmission path needs to be blocked for treatment.
2、 Technical measures for noise control
1. Blockage of transmission path
Sound insulation cover design
Structure: Double layer steel plate with damping layer (thickness ≥ 50mm) is used, and sound-absorbing cotton (density ≥ 48kg/m3) is laid on the inner wall.
Performance: Sound insulation ≥ 35dB (A), soundproof louvers are installed at the opening (insertion loss ≥ 20dB).
Silencer configuration
Type: Impedance composite muffler, with noise reduction frequency range covering 125-8000Hz.
Parameters: Noise reduction ≥ 25dB (A), pressure loss ≤ 800Pa, suitable for dusty/humid gases.
Tubing wrap
Material: 50mm thick glass wool+0.5mm aluminum foil, wrapped with a restraining damping layer on the outer layer.
Effect: Reduce pipeline radiated noise by 10-15 dB (A).
2. Equipment body optimization
Dynamic balance of impeller
Standard: Dynamic balance accuracy G1.6 level, residual unbalance ≤ 0.5g · mm/kg.
Method: Laser calibration+weight adjustment to reduce vibration amplitude by more than 50.
gap adjustment
Impeller clearance: Control single-sided clearance of 0.15-0.25mm, total clearance ≤ 0.5mm.
Gear backlash: Adjust to 0.12-0.18mm, contact spot ≥ 75.
Bearing upgrade
Selection: C3 group clearance cylindrical roller bearings are used, with a rated life of ≥ 80000 hours.
Lubrication: forced circulation lubrication system, oil temperature ≤ 65 ℃, regular oil quality testing (ISO 4406 standard).
3. Basic vibration reduction treatment
Selection of shock absorbers
Type: Rubber isolator (natural frequency ≤ 5Hz) or air spring.
Parameters: Bearing capacity ≥ 1.5 times the weight of the equipment, dynamic stiffness ≤ 0.5kN/mm.
Floating foundation
Structure: Reinforced concrete+50mm thick elastic damping pad, resonance frequency ≤ 8Hz.
Effect: Reduce vibration transmission rate by more than 70%.
3、 Verification of governance effectiveness
acoustic test
Measurement point arrangement: Place points in 4 directions at a distance of 1m and a height of 1.2m from the fan.
Standard: ≤ 85dB (A) during the day and ≤ 80dB (A) at night (in accordance with GB 12348-2008).
Vibration Monitoring
Indicator: Bearing seat vibration speed ≤ 4.5mm/s (ISO 10816-3).
Energy Efficiency Assessment
Parameters: After treatment, the loss of air volume is ≤ 3, and the increase in shaft power is ≤ 2.
4、 Typical Case Analysis
Treatment of a certain sewage treatment plant
Problem: Two 185kW Roots blowers with a noise level of 102dB (A), affecting the surrounding residential areas.
Solution: Install soundproof hood+inlet and outlet mufflers+floating foundation.
Effect: Noise reduction of 32dB (A), noise value ≤ 70dB (A), annual electricity cost savings of 120000 yuan (through frequency conversion transformation).
Governance of a certain cement plant
Problem: The noise of the raw material conveying fan is 110dB (A), and the dust pollution is severe.
Solution: Adopt explosion-proof soundproof hood, anti condensation muffler, and positive pressure ventilation system.
Effect: Noise reduction of 38dB (A), dust leakage rate ≤ 5mg/m3.