The Roots blower cannot be turned (unable to manually turn or stuck when starting) is a serious fault and needs to be stopped immediately for inspection. The following are systematic causes and solutions for faults:
---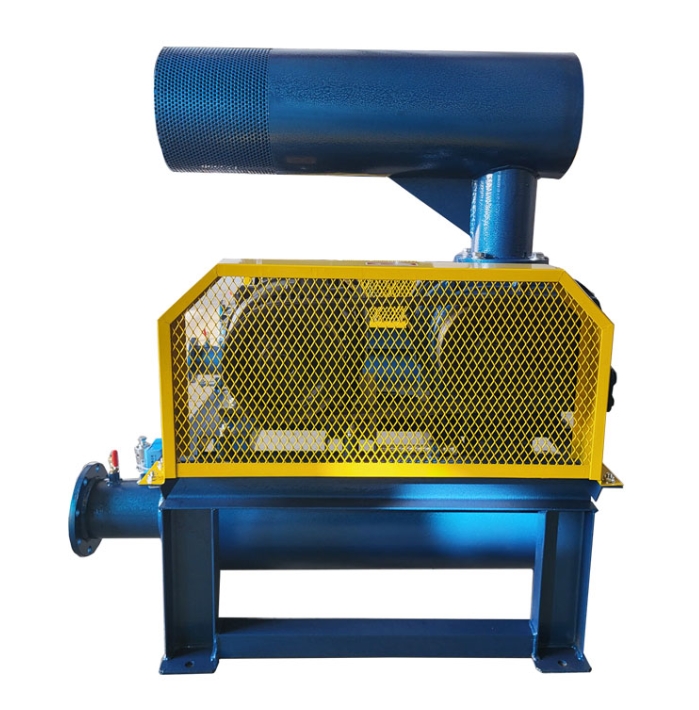
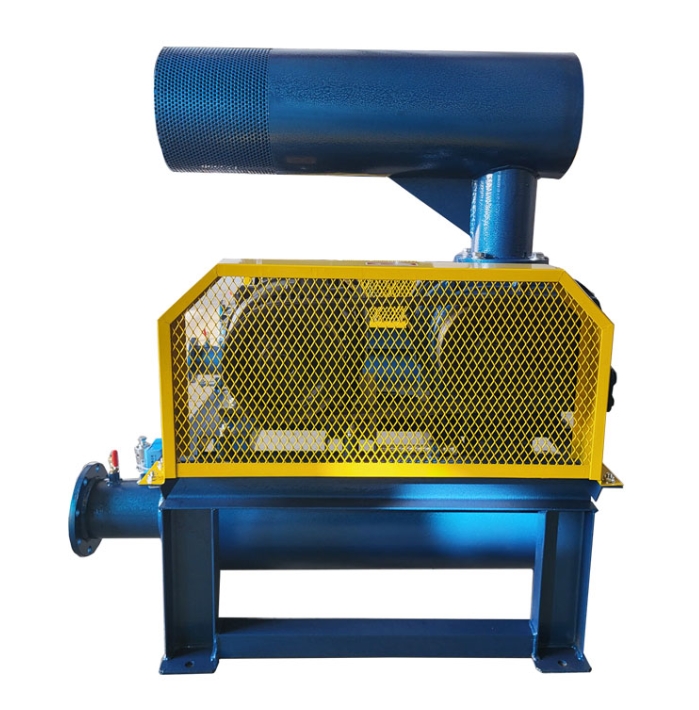
**1、 Root causes and solutions for core faults**
1. Mechanical jamming (most common)**
-Possible reasons:
-Direct friction between impeller and shell (clearance disappears)
-Bearing damage (breakage, retainer detachment)
-The gears inside the gearbox are stuck due to biting
-* * Handling method * *:
-* * Disassembly and inspection * *: Disassemble the coupling → gearbox → end cover in sequence, and observe the wear marks
-Replace components:
-Bearings (such as NSK 6311/C3)
-Gears (need to be replaced in pairs)
-Sealing components (to prevent secondary damage)
-* * Gap Adjustment * *: After reinstallation, ensure that the impeller clearance is 0.2-0.4mm (measured with a feeler gauge)
2. * * Foreign objects enter the cavity**
-* * Typical foreign object * *:
-Bolt/nut (left over from maintenance)
-Welding slag (uncleaned after pipeline construction)
-Scaling and detachment (chemical medium deposition)
-* * Urgent handling * *:
-Open the inspection hole or end cap to remove foreign objects
-Use an endoscope to examine concealed areas
-Install imported filters (≥ 40 mesh)
3. Lubrication system failure**
-* * Fault Symptoms * *:
-The bearing seat turns blue (due to high-temperature burning)
-Gear tooth surface roughening
-* * Solution steps * *:
-Replace lubricating oil (ISO VG220 heavy-duty gear oil)
-Clean the oil circuit (including the cooler)
-Check if the oil pump is working (for forced lubrication models)
4. * * Corrosion caused by long-term shutdown**
-* * Preventive treatment * *:
-Rust prevention treatment is required for downtime exceeding one month:
-Spray anti rust oil inside the cavity
-Manual turning 90 ° per week
-Rusted fan:
-Soak in kerosene for 48 hours
-Copper rod lightly tapping on impeller loosens
---
**2、 Step by step diagnostic process**
```mermaid
graph TB
A [Fan not turning] -->B {Manual turning attempt}
B -->| Stuck | C [Disassemble and inspect mechanical components]
B -->| Effortless but movable | D [Check lubrication system]
C -->E {foreign object found}
E -->| Yes | F [Test drive after cleaning]
E -->| No | G [Check bearings/gears]
D -->H {Is the oil quality normal}
H -->| No | I [Replace lubricating oil]
H -->| Yes | J [Check alignment]
```
---
**3、 Key maintenance precautions**
1. * * Disassembly specifications * *:
-Use a puller to disassemble the bearing (do not directly strike the shaft head)
-Gears need to be marked with matching marks (to avoid misalignment)
-Sealing glue for shell joint surface (Loctite 515)
2. * * Accuracy requirements * *:
-Bearing installation temperature difference method (heated to 80 ℃)
-Gear backlash 0.10-0.15mm (measured with a dial gauge)
-Coupling alignment error ≤ 0.05mm
3. * * Test Standards * *:
-Run without load for 1 hour:
-Bearing temperature ≤ 70 ℃
-Vibration value ≤ 4.5mm/s (RMS)
---
**4、 Preventive maintenance recommendations**
|* * Cycle * * | * * Maintenance Content * *|
|----------|--------------|
|Daily | Check oil level/abnormal noise|
|Monthly | Manual turning test|
|Quarterly | Lubricant analysis|
|Annual inspection gap|
---
**5、 Special working condition handling**
-Transporting viscous media:
-Rinse the chamber with solvent (such as acetone) every week
-Choose an open impeller design
-High temperature environment:
-Install water-cooled jacket (control shell temperature ≤ 120 ℃)
---
**Warning: If the impeller shaft is bent or the shell is cracked, the entire machine must be replaced! Forcefully repairing can lead to accidents. It is recommended to retain the image records of the dismantling and inspection process for the manufacturer's technical analysis.