Direct connected Roots blower is a device that achieves transmission through direct connection between a motor and a fan. Its core advantages are compact structure, high transmission efficiency, and easy maintenance. It is widely used in industrial fields such as sewage treatment, aquaculture, and pneumatic conveying. The following analysis will focus on structural characteristics, technological advantages, application scenarios, and maintenance points:
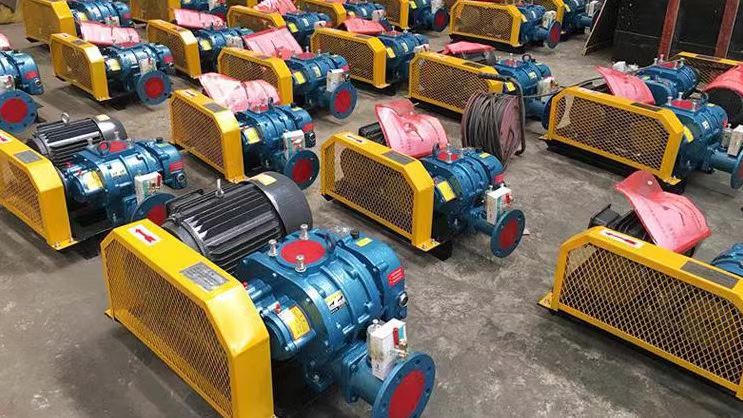
1、 Structural characteristics
Direct transmission design: The motor and fan are directly coupled through a coupling or rigid connection, and the speed is synchronized with the motor. There are no intermediate transmission components such as belts to reduce energy loss.
Compact structure: The fan is designed in a flat shape with a small footprint, making it suitable for installation environments with limited space (such as the narrow machine room of a sewage treatment plant).
Key component optimization: The impeller adopts a three bladed design to reduce airflow pulsation and noise (usually ≤ 85dB (A)); Synchronous gears ensure reverse rotation of the impeller, with clearance accuracy controlled between 0.2-0.4mm to avoid gas leakage.
2、 Technical advantages
drive
The direct transmission efficiency can reach over 95%, significantly higher than belt transmission (efficiency of about 90%), and long-term operation can save energy consumption.
The speed adjustment is flexible and can be achieved through a frequency converter for stepless speed regulation, adapting to different working conditions (such as flow fluctuations in pneumatic conveying).
Stable and reliable
There is no risk of belt aging or slipping, and the failure rate is reduced by about 30%. The maintenance cycle is extended to over 5000 hours.
Vibration value ≤ 4.5mm/s (ISO 10816-3 standard), bearing life can reach 80000 hours (SKF/NSK bearings).
Strong adaptability
It can transport clean air, coal gas, biogas and other media, with a gas temperature range of -20 ℃ to 80 ℃ (high-temperature conditions require the selection of high-temperature resistant bearings and water cooling systems).
Explosion proof products (ExdIIBT4 certification) are suitable for dust explosive environments such as cement plants and flour processing.
3、 Application scenarios
sewage treatment
Provide aeration air to promote the activated sludge treatment process, with a single fan air flow range of 500-50000m3/h and a pressure of 9.8-98kPa, meeting the needs of small and medium-sized sewage treatment plants.
aquaculture
To aerate the aquaculture pond, support high-density aquaculture (such as shrimp and fish), with low noise (≤ 80dB (A)) to avoid disturbing aquatic organisms.
pneumatic conveying
Transporting granular materials such as cement and plastic particles, with a dilute phase conveying concentration of ≤ 10kg/m3 and a dense phase conveying concentration of up to 50kg/m3, and a conveying distance of over 100 meters.
Industrial ventilation
Used for ventilation and air exchange in factory workshops, with a ventilation efficiency of ≥ 90, effectively diluting harmful gases such as VOCs and dust.
4、 Maintenance points
regular inspection
Daily monitoring of oil temperature (≤ 75 ℃), vibration (≤ 4.5mm/s), and current (≤ rated value 80).
Check the quality of the gearbox oil monthly, and replace the lubricating oil (ISO VG 68) when the acid value is greater than 2mgKOH/g or the moisture content is greater than 0.1.
gap adjustment
The total clearance of the impeller should be retested every 2000 hours of operation. If it exceeds the tolerance, it needs to be disassembled and repaired (welding+machining), and the dynamic balance accuracy should reach G2.5 level.
Sealing maintenance
When the mechanical seal leakage exceeds 5mL/h or the oil seal leakage exceeds 10mL/h, it is necessary to replace the fluororubber seal and apply Loctite 587 sealant.
Spare parts Management
Monitoring the life cycle of key spare parts (such as bearings and gears), it is recommended to initiate the procurement process three months in advance to avoid downtime losses.
5、 Selection suggestions
Parameter matching: Determine the air volume (Q), pressure (P), and power (N) according to the working condition requirements. For example, when the air volume required for sewage treatment is 1000m3/h and the pressure is 50kPa, CSR150 fan (motor power 15kW) can be selected.
Environmental adaptation: Double oil tank water-cooled structure is optional for high temperature conditions, and anti-static impellers and copper alloy gears are required for explosion-proof environments.
Energy efficiency optimization: Prioritize the use of variable frequency control models, with a comprehensive energy efficiency ratio (EER) at a load rate of 70-90.