The maintenance of Roots blowers requires systematic testing and targeted repair measures based on their structural characteristics and common types of faults. The following are the maintenance process and key technical points:
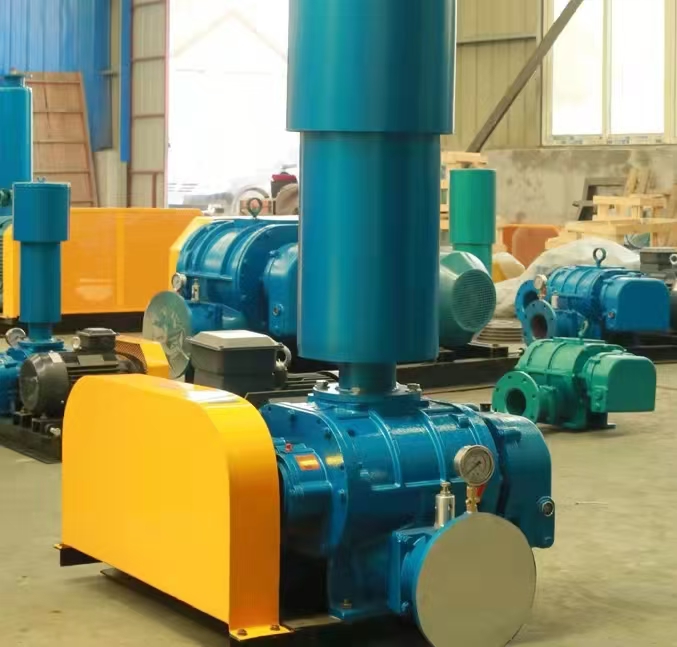
1、 Preparation and specification before maintenance
Power outage and pressure relief
Cut off the power and hang a warning sign to confirm that the fan has stopped running.
Open the vent valve to release system pressure and avoid danger caused by residual media.
Preparation of tools and spare parts
Special tools: torque wrench, laser alignment instrument, lead wire testing kit.
Spare parts list: high-precision bearings (SKF/NSK), gear sets, fluororubber oil seals, anti-wear hydraulic oil (ISO VG 68).
Environmental inspection
Ensure good ventilation, surrounding flammable materials, and equipped with fire extinguishing equipment.
2、 Core fault diagnosis and maintenance technology
1. Bearing and gear system
Fault symptoms: excessive bearing clearance (>0.10mm), abnormal gear backlash (>0.18mm).
Testing method:
Measure the gear backlash with a feeler gauge and check the meshing contact area with red lead powder (≥ 75).
The lead wire method is used to detect bearing clearance, and the laser alignment instrument is used to calibrate the concentricity of the shaft system.
Repair process:
When replacing bearings, check the wear of the bearing seat synchronously and if necessary, drill holes and insert sleeves.
Gear adjustment: The side clearance is controlled at 0.10-0.18mm, the blade clearance is ≥ 0.15mm, and the blade clearance is ≥ 0.30mm.
After assembly, conduct a 2-hour no-load trial run, monitoring vibration values ≤ 4.5mm/s and oil temperature ≤ 75 ℃.
2. Impeller and sealing system
Fault symptoms: impeller clearance exceeding tolerance (>0.6mm), seal leakage.
Testing method:
Impeller clearance: The single-sided axial clearance is 0.12-0.18mm for the front wall panel and 0.63-0.69mm for the rear wall panel.
Sealing inspection: Fluorescent agent penetration method is used to detect oil seal leakage, and a thickness gauge is used to measure the wear of the sealing surface.
Repair process:
Impeller repair: When the clearance exceeds the tolerance, welding and machining are used, and the dynamic balance is verified to G2.5 level.
Sealing replacement: Double lip fluororubber oil seal, apply high-temperature resistant grease during installation, and apply Loctite 587 sealant to the gland bolts.
Sealed chamber pressure test: Fill with 0.5MPa nitrogen and maintain pressure for 30 minutes, with a leakage rate of ≤ 0.1mL/min.
3. Lubrication and cooling system
Fault symptoms: high oil temperature (>80 ℃), deterioration of oil quality.
Testing method:
Oil quality analysis: When the moisture content is greater than 0.1 or the acid value is greater than 2mgKOH/g, it needs to be replaced.
Cooler detection: Infrared thermal imaging instrument checks for pipeline blockage, and pressure gauge tests for water side pressure drop (≤ 0.05MPa).
Repair process:
Lubricating oil replacement: Replace the anti-wear hydraulic oil every 5000 hours, keeping the oil level within ± 5mm of the centerline of the window.
Cooling system cleaning: chemical cleaning agent circulation flushing, neutralization and passivation treatment after acid washing.
Forced ventilation renovation: Install axial flow fans to reduce the inlet temperature to ≤ 40 ℃.
3、 Review of key performance parameters
vibration and noise
Vibration value ≤ 4.5mm/s (ISO 10816-3 standard), noise ≤ 85dB (A) (at a distance of 1m from the equipment).
Gap retest
The total clearance of the impeller is 0.2-0.4mm, the side clearance of the gear is 0.10-0.18mm, and the contact area is ≥ 75.
Sealing performance
Mechanical seal leakage rate ≤ 5mL/h, oil seal leakage rate ≤ 10mL/h.
Efficiency verification
No load current ≤ rated value 80, load efficiency ≥ 75 (under standard conditions).
4、 Preventive maintenance strategy
periodic testing
Daily: Record oil temperature, vibration, and current.
Weekly: Gearbox oil quality inspection, belt tension inspection (sinking amount 10-15mm).
Monthly: Air filter cleaning (replace filter element when pressure difference>500Pa).
Annual major overhaul
Disassembly inspection: rotor dynamic balance, gear meshing surface wear, bearing running in marks.
Repair process: laser cladding repair gear tooth surface, plasma spraying repair shaft neck.
Spare parts Management
Key spare parts life monitoring: 5 years for bearings, 8 years for gears, and 2 years for seals.
Establish a spare parts lifespan ledger and initiate the procurement process three months in advance.
5、 Typical Cases and Effects
Case: The Roots blower in a sewage treatment plant has a noise level of 95dB (A) and a vibration of 8mm/s.
Diagnosis: Gear backlash is 0.25mm (exceeding 40%), and the inner ring of the bearing is worn.
Repair: Replace the gear set (with side clearance adjusted to 0.12mm) and SKF 6311 bearings.
Effect: Vibration reduced to 3mm/s, noise reduced to 82dB (A), and operating life extended to 8 years.