The air volume of Roots blower can be adjusted, but the adjustment method is significantly different from that of centrifugal blower and other models. The core principle is based on the volumetric forced gas delivery characteristic, which indirectly controls the flow rate by changing the rotor speed or pressure relief path, rather than directly changing the internal structure of the fan. The following analysis will focus on the principles of regulation, common methods, applicable scenarios, and precautions:
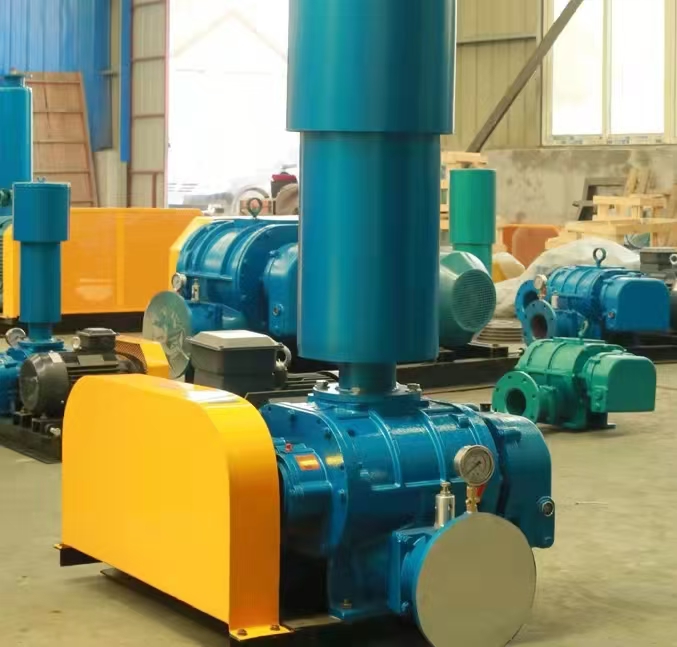
1、 Principle of air volume regulation for Roots blower
The Roots blower rotates synchronously in reverse through two three bladed rotors, forming a periodic compression chamber inside the cylinder to achieve constant volume flow of gas delivery. The air volume adjustment should be based on the following characteristics:
Linear relationship between speed and flow rate: The air volume (Q) is strictly proportional to the speed (n) (Q=k · n, k is a constant) and is affected by pressure fluctuations.
Forced exhaust characteristic: Even if the outlet is blocked, the fan will still operate at the rated volume flow rate, causing pressure to rise rather than flow rate to decrease.
2、 Common methods and comparison of air volume adjustment
Adjustment Method Implementation Principle Adjustment Range Response Speed Energy Consumption Impact Typical Application Scenarios
Variable frequency speed regulation uses a frequency converter to change the motor frequency, adjust the rotor speed, and continuously adjust it. When the speed drops, the energy consumption decreases by milliseconds, and the square level is reduced. It is necessary to control the air flow in processes such as sewage treatment aeration and pneumatic conveying, as well as frequent start stop conditions such as intermittent gas supply
Bypass valve regulation diverts some gas through the bypass pipeline, reducing effective output from 0 to rated flow rate. Continuous regulation of second level bypass gas waste leads to an increase in energy consumption. Temporary flow adjustment (such as during commissioning phase) allows for energy loss scenarios (such as ventilation system auxiliary regulation)
Inlet throttling regulation is achieved by controlling the opening of the air inlet through a valve, which can change the suction resistance. Limited regulation (prone to surge) can result in a second level throttling loss, leading to an increase in energy consumption and requiring rapid response to emergency conditions (such as transient pressure reduction in explosion-proof systems). However, this can easily cause surge and should be used with caution
Multiple parallel controls are implemented through the combination of starting and stopping different numbers of fans to achieve step-by-step regulation, discrete multi-level regulation, minute level shutdown, and zero energy consumption of fans in large-scale systems (such as pneumatic conveying in cement plants and large-scale sewage treatment plants), which need to be adjusted according to load classification scenarios
Mechanical speed regulation changes the transmission ratio by replacing pulleys or gear pairs. Fixed gear adjustment requires shutdown, and changes in transmission efficiency affect energy consumption. Long term fixed working conditions for coarse adjustment (such as in the early stages of equipment renovation) and upgrading of old equipment without variable frequency control conditions
3、 Selection of adjustment methods in different scenarios
Prioritize frequency conversion speed regulation:
High precision control: scenarios that require real-time matching of process parameters such as dissolved oxygen concentration and material conveying speed.
Energy saving demand: systems that operate for a long time and have large load fluctuations (such as aeration tanks in sewage treatment plants with large temperature differences between day and night).
Equipment protection: To prevent fan overload or pipeline rupture caused by excessive pressure.
Applicability of bypass valve regulation:
Emergency backup: Temporary replacement in case of frequency converter failure.
Extensive control: In situations where energy consumption is not sensitive and flow accuracy is low (such as ordinary ventilation systems).
Limitations of inlet throttling regulation:
Surge risk: When the throttle opening is less than 30 degrees, the fan may enter an unstable working zone, causing increased vibration or even damage.
Energy consumption degradation: The throttling pressure drop is converted into ineffective heat energy, resulting in poor long-term economic performance.
4、 Key considerations during the adjustment process
Pressure boundary:
Before adjustment, it is necessary to confirm the allowable pressure of the system (usually 1.1 times the rated pressure of the fan) to avoid accidents caused by overpressure.
It is recommended to install pressure sensors and interlock protection devices, which will automatically trigger frequency conversion or bypass valve opening when the pressure exceeds the threshold.
Surge avoidance strategy:
When adjusting the inlet throttle, it is necessary to maintain a valve opening of ≥ 40, or set the speed limit through a frequency converter (usually 60% of the rated speed).
For conditions prone to surge, a composite control scheme of variable frequency speed regulation and bypass valve can be adopted.
Energy efficiency optimization techniques:
When using variable frequency speed regulation, avoid long-term operation at low frequencies below 30Hz (which can easily cause severe motor heating).
Multiple parallel systems should adopt a hybrid control mode of "frequency conversion dominant+fixed speed supplement" to reduce the number of starts and stops of fixed speed fans.
5、 Customized adjustment plan for special working conditions
Pulse gas supply demand:
Solution: Combination of frequency converter and high-speed solenoid valve, intermittent gas supply is achieved through short-term high-frequency pulses (such as pulse cleaning in pneumatic conveying).
Advantages: Compared to mechanical valve switching, the response speed is increased by 90 and energy consumption is reduced by 30.
Corrosive gas treatment:
Solution: Full frequency control+corrosion-resistant coating rotor to avoid throttling valve jamming caused by medium crystallization.
Case: After adopting this plan, the equipment maintenance cycle of a chemical plant was extended from 3 months to 18 months.
Summary: The air volume regulation of Roots blowers needs to be comprehensively decided based on process requirements, energy consumption targets, and equipment characteristics. Variable frequency speed regulation has become the mainstream solution due to its precision, energy efficiency, and reliability. However, in specific scenarios, traditional methods such as bypass valves and multi machine parallel connections still have practical value. It is recommended to prioritize intelligent frequency converters that support communication protocols such as Modbus to achieve seamless integration with DCS/PLC systems and reserve expansion space for subsequent process optimization.