The Roots blower coupling is an important component that connects the motor and the fan shaft, directly affecting the operational stability and efficiency of the equipment. The following analysis will be conducted from three dimensions: type selection, application adaptation, and installation and maintenance:
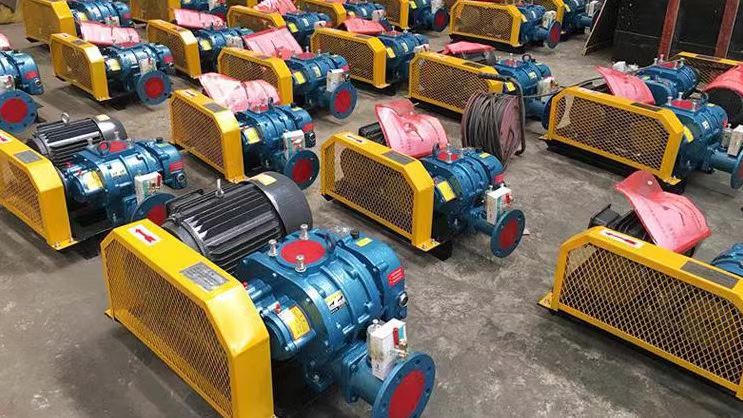
1、 Type selection: Elastic coupling vs. Rigid coupling
Elastic coupling: Compensates for small displacements between shaft systems through the deformation of elastic components (such as rubber and polyurethane), absorbs vibrations and impacts, and is suitable for scenarios with large speed fluctuations or high requirements for shock absorption (such as frequently started and stopped sewage treatment aeration systems). Its advantage is that it can reduce bearing wear and extend machine life, but it is necessary to regularly check the aging of elastic components.
Rigid coupling: With a simple structure and high torque transmission efficiency, it is suitable for high-speed and high-precision centering working conditions (such as continuous and stable operation of chemical raw material conveying systems). Its advantage lies in the absence of elastic component loss, but it is necessary to ensure that the coaxiality error between the motor and the fan shaft is ≤ 0.05mm, otherwise it may cause increased vibration.
2、 Application adaptation: Matching working condition parameters with couplings
High temperature environment: If the operating temperature of the fan exceeds 80 ℃, a high-temperature resistant coupling (such as a metal diaphragm type) should be selected to avoid the failure of the elastic body. For example, in the treatment of exhaust gas in cement plants, it is necessary to prioritize the use of rigid couplings with insulation sleeves.
High dust scenario: When the dust concentration is ≥ 100mg/m3, a coupling with a sealed structure should be used to prevent particle intrusion and wear. For example, the pulp conveying system of a paper mill needs to be equipped with double-layer sealed elastic couplings.
High speed operating conditions: When the speed exceeds 3000rpm, a coupling with dynamic balance accuracy of G2.5 level should be selected to reduce vibration noise. For example, in the pneumatic conveying of fine chemical raw materials, lightweight aluminum alloy rigid couplings are required.
3、 Installation and Maintenance: Key Steps and Fault Prevention
Installation alignment: Use a laser alignment instrument to ensure that the coupling end face runout is ≤ 0.02mm and the radial deviation is ≤ 0.03mm. For example, in the exhaust gas treatment project of a refinery, the vibration value of the fan exceeded the standard due to the misalignment of the coupling, and the fault needs to be readjusted.
Regular inspection: Check the tightening torque of the coupling bolts every 2000 hours of operation (torque value deviation ≤± 5), and measure the radial clearance (standard value 0.1-0.3mm). For example, a sewage treatment plant experienced a fan shaft fracture accident due to the failure to replace worn elastic couplings in a timely manner.
Lubrication management: High temperature resistant lithium based grease (operating temperature range -30 ℃ to 150 ℃) is used, replenished every 500 hours of operation to ensure sufficient lubrication of the bearings inside the coupling.