**Guidelines for handling stuck faults of Roots blower**
The Roots blower is stuck (unable to be manually turned or stuck during startup), which is a serious mechanical failure that requires systematic investigation and handling. Here is a detailed solution:
---
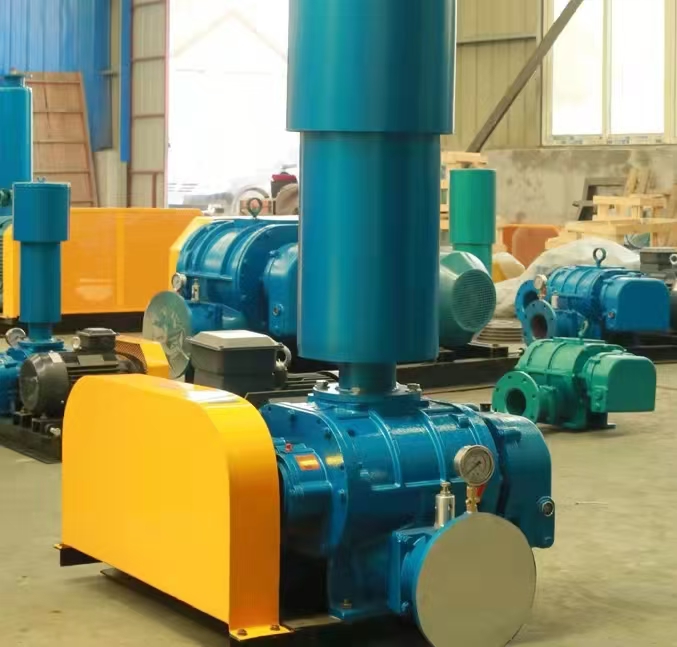
**1、 Emergency handling steps**
1. * * Immediately cut off power**
-Cut off the power and lock it with a tag (LOTO) to prevent accidental startup.
2. * * Pressure relief operation**
-Open the exhaust valve to release pipeline pressure and avoid disassembly under pressure.
3. * * Try manual turning**
-Rotate the coupling or pulley with a wrench:
-* * Can rotate slightly * * → There may be local friction or poor lubrication.
-* * Stuck * * → Mechanical components damaged or foreign objects entering.
---
**2、 Fault causes and corresponding solutions**
**1. Foreign object gets stuck in the cavity**
-Common foreign objects: bolts, welding slag, sealing fragments, and medium crystallization.
-* * Handling method * *:
-Open the inlet and outlet flanges and inspection holes, and use an endoscope to explore.
-Use a magnetic rod to suck up metal foreign objects, and lightly tap the impeller with a copper rod to loosen it.
-* * Preventive measures * *:
-Install a Y-shaped filter (aperture ≤ 5mm).
-Seal the pipeline opening during shutdown maintenance.
**2. Friction between impeller and shell**
-* * Reason * *:
-Bearing wear causes the rotor to sink.
-Impeller thermal deformation or coating detachment.
-* * Processing * *:
-Measure the impeller clearance (standard 0.2~0.4mm), adjust if it exceeds the tolerance:
-Replace bearings (such as SKF 6312).
-Repair the impeller (dynamic balancing treatment after welding).
-Attention: Do not use sandpaper to polish the impeller!
**3. Bearing/gear damage**
-Diagnostic features:
-The bearing seat heats up (>90 ℃).
-The gearbox has metal debris.
-* * Replacement process * *:
1. Remove the coupling or pulley.
2. Use a hydraulic puller to pull out the damaged bearing.
3. Heat the new bearing to 80 ℃ before installation (direct tapping is prohibited).
4. Gears need to be replaced in pairs and coated with molybdenum disulfide grease.
**4. Lubrication failure**
-* * Checkpoint * *:
-Is the oil level below the mark.
-Whether the lubricating oil is emulsified or contains impurities.
-* * Processing * *:
-Clean the oil tank and replace the lubricating oil (recommended ISO VG220).
-Check if the oil pump and oil circuit are blocked.
**5. Long term shutdown rusting**
-* * Card removal method * *:
-Inject kerosene into the chamber and soak for 24 hours.
-Alternating forward and backward light disc impellers, gradually loosening.
-Severe corrosion requires replacement of the rotor assembly.
---
**3、 Key points for assembly after maintenance**
1. * * Gap adjustment**
-Use a feeler gauge to measure the clearance between multiple points of the impeller, with an error of ≤ 0.05mm.
-Axial displacement ≤ 0.10mm (detected by dial gauge).
2. * * Sealing treatment**
-Apply high-temperature resistant sealant (such as Loctite 510) on the joint surface.
-Install the oil seal lip inward (leak proof).
3. * * Alignment correction**
-Laser alignment of coupling (deviation ≤ 0.05mm).
-Check the tension of the belt during transmission (with a sinking of 5-8mm).
---
**4、 Test run and acceptance criteria**
1. * * No load trial operation**
-Tap 3 times to confirm correct steering.
-Run for 30 minutes, monitor:
-The bearing temperature is less than 70 ℃.
-Vibration value<4.5mm/s.
2. * * Load testing**
-Gradually increase the voltage to the rated value and check:
-Whether the current exceeds the standard.
-Is there any abnormal noise.
---
**5、 Preventive maintenance recommendations**
-* * Daily check * *:
-Record oil level, temperature, and vibration daily.
-* * Regular maintenance * *:
-Replace the lubricating oil every 500 hours.
-Inspect the clearance and gear wear every year.
-Long term shutdown:
-Drain the lubricating oil and inject anti rust oil.
-Manually rotate 180 degrees per month.
---
**6、 Risk Warning**
-* * Prohibited operation * *:
-Forcefully starting the stuck fan can cause the shaft to break.
-Heating bearings with flames (risk of deformation).
-* * Scenarios that must be replaced * *:
-Impeller cracks or shaft bending.
-Severe wear and tear (>1mm groove marks) inside the shell.
---
**Tip: If you lack professional tools or experience, it is recommended to contact the manufacturer's service engineer for assistance. Keeping the image records during disassembly can help with fault analysis!